Binding
Binding is generally considered to be the process of fastening the sheets of a publication in the proper order and most often within a protective cover.
There are various methods of binding available that can be selected for the type of publication and/or for the type of handling it will receive.
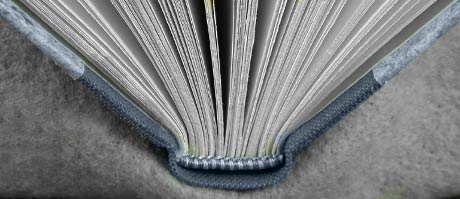
Perfect Binding
Perfect binding is one of the most commonly used binding methods. It is used for many types of publications.
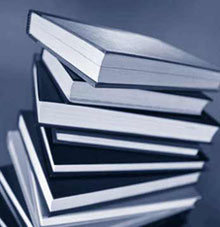
Pages for a perfect bound publication are gathered, stacked, and placed in special equipment where the binding edge is covered with glue. A cover is then attached to the book to complete the process.
This method is most successful when the paper grain runs parallel with the spine of the book. Magazines and books may have the title and other information printed on the flat spine of the cover.
Perfect binding is one of the most automated of the binding methods. It can be divided into three main categories: hot adhesive, cold adhesive, and thermal binding.
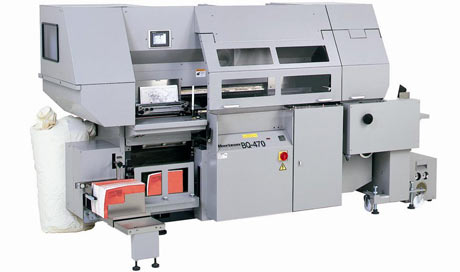
Hot Adhesive Perfect Binding
Hot glue is the most widely used of the perfect binding adhesives. Books are usually 1/4” up to 2 1/4” thick depending on the thickness of the substrate. A major disadvantage with hot adhesive is that the book cannot lie flat when it is open. The binding will break if too much pressure is applied in attempting to make the book lie flat when it is open.
Cold Adhesive Perfect Binding
Cold glue is not used as often as hot glue because it is more expensive and requires more time to cure than hot glue, but it is stronger and more flexible.
When the cold adhesive is used in conjunction with a scored and hinged cover, the book is able to lie flat when it is open without cracking the binding. Books with perfect bindings made with cold adhesive range in thickness from 1/8” to 2 1/4”.
Thermal Binding
Thermal binding is similar to the hot adhesive method of perfect binding in that adhesive and heat are used to form the binding, but instead of hot glue, an adhesive strip is used.
Pages are fed into a machine where an adhesive strip attached to a wrap around cover is applied to the binding edge of the pages. Heat is applied so that the adhesive strip and cover are adhered to the pages.
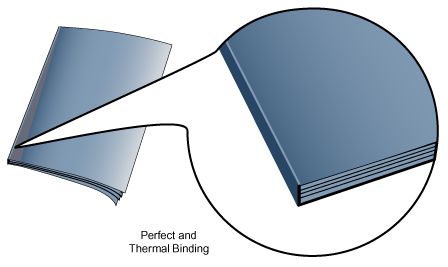
Plastic Comb Binding
Plastic combs are another binding method that allow for the addition or removal of pages from a book. The system involves punching rectangular holes into pages, which are then slid over the fingers of the plastic comb.
A standard 11” sheet would have 19 holes punched into it. The plastic combs are durable and come in a variety of colors. Book titles or descriptions can be printed on the spine of the plastic comb so that the book can be identified when it is being stored.
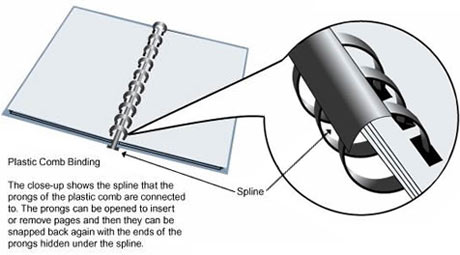
Spiral
A spiral binding consists of a continuous wire, which is coiled through evenly spaced holes that have been punched into the pages of a book.
The spiral wire can be made of metal, plastic, or plastic coated metal. Plastic is available in a variety of colors, but the metal spiral has a limited color selection.
When the books are open, the pages lie flat. The pages can also be folded over completely, which makes spiral binding a good choice for training manuals, cookbooks, notebooks, and calendars.
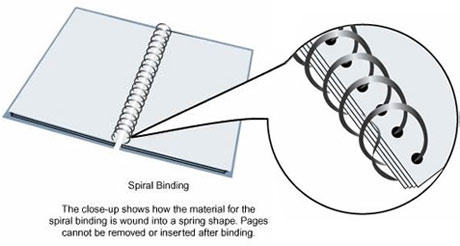
Double Loop Wire Binding
Double loop wire binding consists of a series of double wire loops from a continuous pre-formed wire, which are inserted into pages that have been punched with square or round holes.
The loops of the wire are held opened by a machine to allow the pages to be inserted over the loops. Once the loops are closed, extra pages cannot be added.
Double loop wire works best for books of one-inch thickness or less. Many technical manuals and cookbooks have this type of binding and they are very popular among architects.
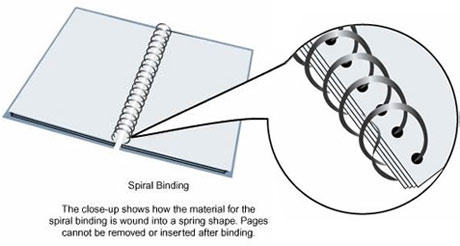
Double loop wire binding is also known as “Wire-O-Binding”. Listed below are the types of wire available.
- 3:1 Wire: With this wire, the paper is punched 3 holes per inch, which is 32 holes per standard 11” sheet size. It is available in sizes ranging from 3/16” up to 9/16” in diameter. It has the best appearance of all double loop wire.
- 2:1 Wire: Pages are punched with 2 holes per inch or 21 holes per standard 11” sheet size. 2:1 wire is used for binding books that are too large for 3:1 wire and is available in sizes ranging from 5/8” to 1”. The wire is more durable and sturdy than 3:1 wire.
- 19 Loop: The pages are punched with 19 rectangular holes per standard 11” sheet size and the wire comes in diameters ranging from 1/4” to 1”. The wire is similar in appearance to 2:1 wire.
Loose Leaf
Loose Leaf Binding is one of the simplest methods of binding. Cut pages are punched with holes to accommodate the rings or posts contained in the binder. An advantage to both ring or post binders is that pages can be added or removed easily.
The ring binder also has the advantage of allowing the pages to lie flat when the book is open, making it a good choice for technical or training manuals. An allowance for the inner margin (gutter) must be made to allow for the holes that are punched in the pages.
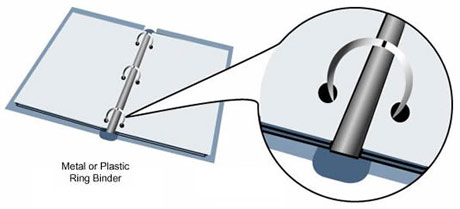
Post Bind
Binds a group of loose leaf sheets using a screw and post inserted through the holes that are punched in the sheets.
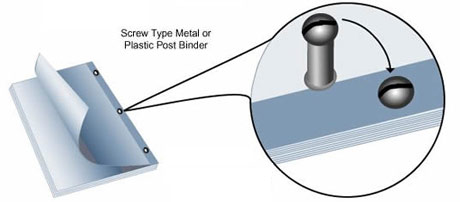
VeloBind®
There is only one manufacturer for this type of binding, so it is a trademarked brand name. Security strips are used for the binding of pages and it is most often used for legal documents and publications. The equipment used for this type of binding is expensive. Pages cannot be added or removed unless the security strip is cut.
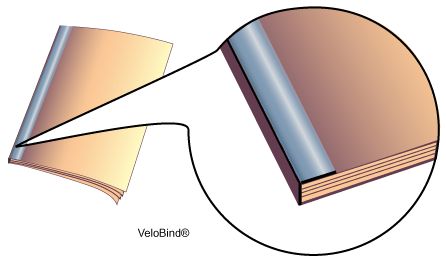
Saddle Stitching
Saddle stitched books are constructed with sheets that are printed front and back that represent four pages of a book. The sheets of four pages are stacked with other sheets in the correct page order and then stapled along the fold line or saddle.
The stapling is accomplished on equipment that cuts staples from a continuous roll of wire mounted on the machine and inserts them into the paper. Some machines can do the folding and stitching in one operation. Many booklet manufacturers use this multiple task equipment to increase efficiency.
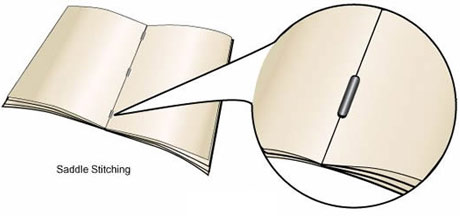
Saddle stitched binding can work for volumes up to 128 pages (32 sheets, printed with 2 pages front and back) if the paper stock is thin enough, but it just isn’t practical for anything larger. The larger the quantity of sheets, the greater the problem with a phenomenon called page “creep”.
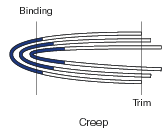
Creep refers to the inner sheets sticking out further than those closer to the outside, because of the paper thickness. To compensate for this, the pages are “shingled”, which means that the inner margin, or “gutter”, is increased on the pages working from the inside of the book to the outside.
Side Wire Stitching
Instead of staples being inserted into the side or saddle of the pages, staples are inserted into the top of the gathered sheets or pages and pressed down vertically until reaching the back side of the booklet. It is often used as a means to bind a larger quantity of sheets together than can be saddle stitched.
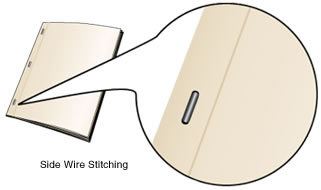
Loop Stitching
Loop stitching is a form of binding where the stitches (staples) form a loop that can be used to hold the book in a binder (such as a standard 3 ring binder).
Loop stitching is basically the same method of binding as saddle stitching, however a special stitching head is used that produces a loop in the outside portion of the stitch. With this type of binding books can be put into binders without the need of drilling.
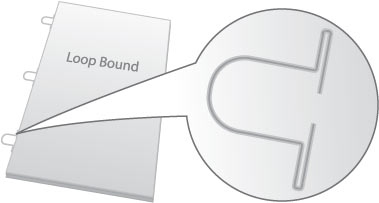
Sewn Case Binding
Sewn case binding, also known as “edition binding”, is the most expensive binding method, but is the most durable. It can be used for any book thickness, but the most common thicknesses range from 1/4” up to 3”.
A number of steps are required to complete a sewn case bound book, so the process is very automated.
- A large printed sheet containing 16 or 32 individual book pages, called a signature, is cut apart, folded, and assembled in the correct page order.
- The signature is sewn together with other signatures.
- Endleave papers, which are usually made of heavier stock than the other pages of the book, are glued to the outside of the first and last signatures.
- The book is trimmed on three sides.
- The sewn edge (spine) of the book is coated with glue.
- The spine of the book is rounded in a machine to allow the cover of the book to function properly when it is attached.
- A strip of gauze is wrapped around the spine of the book.
- The cases (covers) that will be used for the book are made from heavy board stock with its grain running parallel to the spine of the book to prevent warping of the cover. The heavy board cases are wrapped with embossed paper, cloth, plastic coated material, leather, or other materials to form the final covering.
- The book is attached to its hard case/cover on a casing-in machine, which glues the endleave papers to the case.
- The final step is to insert the book into a hydraulic press to ensure that it dries properly and does not warp.
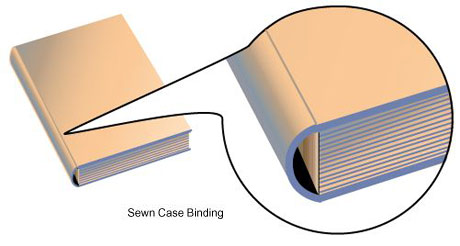
Sewn Soft Cover
Occasionally the pages of a book are attached to paperback or soft covers with the use of strong thread, which is sewn through the pages and cover using special equipment.
This binding method is often preferred for technical manuals and textbooks, which may be handled often by a number of people. It is more durable than perfect binding or wire binding where the overuse of a book may cause the binding to fail at a faster rate.
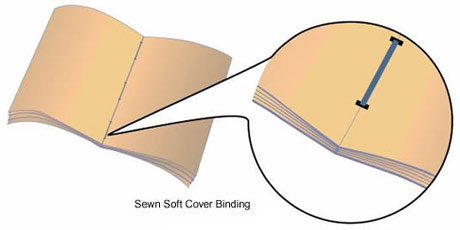
Common Cover Types
Two of the most popular types of covers used for saddle stitched booklets are the standard cover and the self cover.
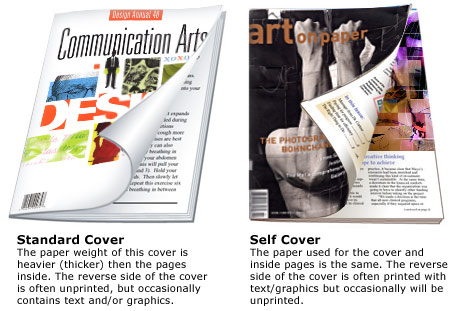
Padding
Some printed applications are padded into tablets or booklets with the use of an adhesive applied to one edge of a group of sheets.
Padding techniques are actually a form of binding, but the resulting pad or booklet is not intended to remain permanently bound – the padded edge serves only to keep the sheets together until a sheet is used and then detached from the padded edge.
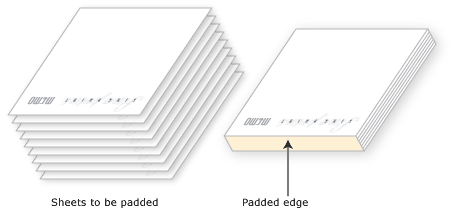
Most of the padded products begin as single sheet items, which are then gathered and padded into various quantities to create note and memo pads, prescription pads, coupon pads, and many other similar applications.
The padding compound is usually a type of glue, which dries to a soft or semi-hard consistency. There are various types of glue used, such as varieties applied manually as a cold application and other varieties applied by machine as a hot melt application.
Note: Your vendor may have limitations on the number of sheets that can be padded as well as the minimum and maximum paper weights that can be manufactured into pads.
Cold Glue Application
The following steps are common for most padded applications using cold glue:
- A large quantity of single sheets is stacked into a pile.
- Chipboard or some type of heavy paper is inserted at designated intervals, which serves as a backer material and gives the pads stability.
- The pile of sheets and pad backers are carefully jogged and precisely stacked to create a smooth edge for the application of the glue. The entire stack is jogged toward the side where the padding compound is to be applied.
- A standard paintbrush is used to apply the glue to the stack of sheets.
- After the glue is applied to the smooth edge of the stack, weight is applied to the top of the stack or the entire stack is clamped into a device called a padding press.
- When the glue has dried, the weight or clamp is removed.
- A knife is inserted into the large stack along the bottom of each piece of backer material in order to cut the glue and create the individual pads.
Hot Melt Application
For padded applications using hot melt adhesive, automated equipment speeds up the process. The circular or carousel padder is one of the most popular padding machines used for this type of application.
The following steps are typical for hot melt applications using the circular or carousel padding machine:
- The single sheets are placed into stacks of 25, 50, 100 or an amount representing the quantity of sheets required per pad. Automated equipment is often used to count the sheets into the correct quantity per pad.
- Each stack of sheets is combined with a backer sheet of chipboard or heavy paper.
- The carousel padder has several identical clamping units, which pass by a staging area as the machine rotates. From the staging area, the operator inserts a stack of sheets, with a backer, into each clamping unit.
- The clamping units have mechanisms that jog the single sheets and backer material into an even pile before the pad is clamped together.
- The clamping units pass over a drum that applies the hot glue to the edge of the clamped pad. The hot melt glue dries very quickly after it is applied.
- After a short interval, the clamping unit releases the pad, which falls onto a conveyor belt where it is retrieved and packaged.
These steps represent one revolution of the carousel machine. The speed of the carousel can be increased or reduced to accommodate the skill level of the operator in their ability to insert the pads into each clamping unit.
Note: Products padded with a hot melt glue and exposed to high temperatures in storerooms or car trunks, may develop a cracking or degumming of the adhesive causing the padded sheets to separate from the padding adhesive. Cracking or degumming of the adhesive will not occur with cold glue adhesives.