Materials and Stocks
Substrate is a term used to describe the base material onto which images will be printed. Base materials include (though are not limited to) papers, fabric, plastics, foils and films.
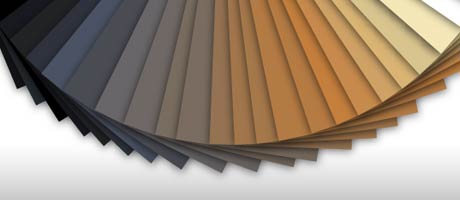
Of all available substrates, paper choice is an underlying consideration in almost every printing job. Since it influences the design and is factored into many prepress decisions, we will focus most of our attention on paper.
The Paper Process
Step 1: Forestry & Recycling
Typically, trees used for papermaking are specifically grown and harvested like a crop for that purpose. Recycled paper is another important source of paper fiber.
Step 2: Debarking, Chipping
To begin the process, logs are passed through a debarker, where the bark is removed, and through chippers, where spinning blades cut the wood into 1” pieces, which are then pressure-cooked with a mixture of water and chemicals in a digester.
Step 3: Pulp Preparation
The pulp is washed, refined, cleaned and sometimes bleached, then turned to slush in the beater. Color dyes, coatings and other additives are mixed in, and the pulp slush is pumped onto a moving wire screen.
Step 4: Paper Formation
As the pulp travels down the screen, water is drained away and recycled. The resulting crude paper, is squeezed between large rollers to remove most of the remaining water and ensure smoothness and uniform thickness. It is then run through heated dryer rollers to remove the remaining water.
Step 5: Paper Finishing
The finished paper is then wound into large rolls, which can be 30 feet wide and weigh close to 25 tons. A slitter cuts the paper into smaller, more manageable rolls, and the paper is ready for use.
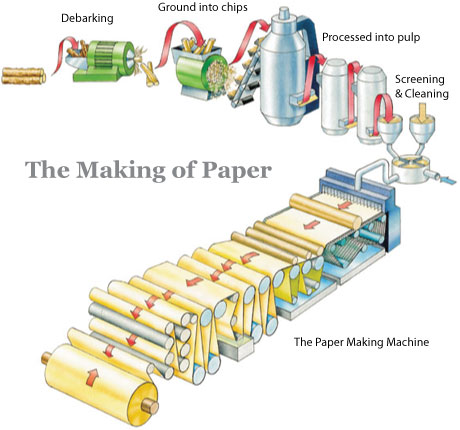
Paper Characteristics
Basic Size and Basis Weight
The basis weight refers to the weight in pounds of 500 sheets of paper when it has been cut to that paper’s standard size. For example the basic size for Bond paper is 17 × 22 inches. If 500 of these sheets weighs 20 pounds, it is classified as 20 lb. bond. The chart below contains some common paper types and their basic size.
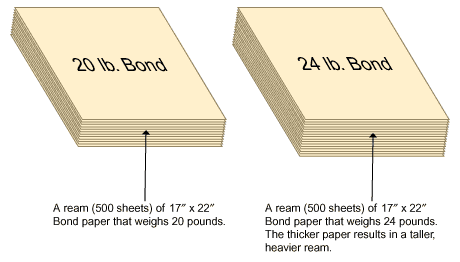
ISO Size Standards
The International Organization for Standardization (ISO) has established standards for paper sizes based on the metric system. The standards have been grouped into three different series of requirements: “A-series”, for general printing, “B-series”, for posters, and “C-series”, for envelopes, postcards, and folders.
The “A” series is the most commonly used with sizes ranging from A0, which is the largest, down to A8. When an A0 sheet is cut in half, two A1 sheets are produced, and when an A1 sheet is cut in half, two A2 sheets are produced, and so on…
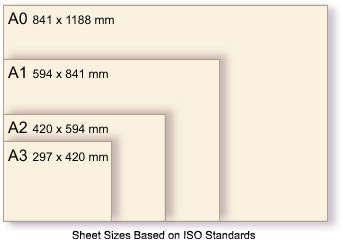
North American Size Standards
Although the ISO size standards are common in many parts of the world where the metric system is the established standard for measurement, North American sheet sizes are based on inches and are shown in the illustration below.
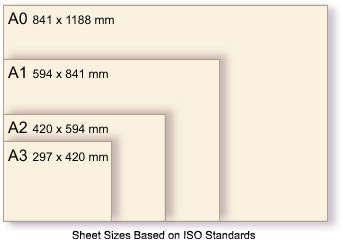
Universal Web Sizes
The paper rolls shown below are the standard widths used on web presses. The illustration also shows the standard ISO sheet sizes and the standard North American sheet sizes that can be obtained from each roll width.
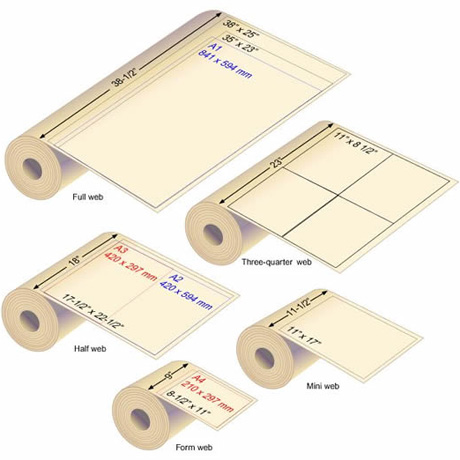
Finish
The finish refers to the surface characteristics of the paper. Finishes can be applied to paper during the manufacturing process or produced offline. Some common paper finishes are described below.
- Cockle – A cockle finish simulates characteristics of hand made paper with a wavy, rippled, puckered finish. The effect is obtained by air drying the paper under minimum tension.
- Felt – Felt is a soft texture on uncoated paper that is created during the papermaking process with a either felt covered roller or with a rubber roller with a felt pattern that creates the finish. It can also be accomplished as an offline process. The felt finish does not affect the strength of the paper.
- Gloss – A gloss finish produces a shiny and reflective surface on one or both sides of certain coated papers. A higher gloss is usually seen on higher quality coated papers. The gloss finish is produced from compounds added during the paper making process.
- Laid – A laid finish has the appearance of translucent lines running horizontally and vertically in the paper. It is produced during the papermaking process with a special roller that creates the pattern in the wet paper.
- Linen – Linen finished paper resembles linen cloth and is usually produced after the papermaking process as an offline embossing process.
- Matte – A finish on certain coated papers that is smooth but gives a dull appearance. A matte finish, as well as other types of coated paper, are good choices for print jobs in which high quality is required.
- Parchment – A paper finish that has an old or antique appearance and is the result of washing sulfuric acid over the paper and then quickly neutralizing the acid wash. This process melts the outer paper fibers which fill the voids in the rest of the paper. Parchment is very durable and grease resistant.
- Smooth – A smooth finish is the result of the paper passing through sets of rollers during the papermaking process. This process is known as calendering.
- Vellum – A vellum finish has an eggshell appearance and is consistent and even but not as much as a smooth finish. Vellum is one of the most popular uncoated finishes and paper with this finish has a high ink absorbency rate.
- Wove – An even finish in uncoated paper with a slight texture made by a felt roller covered in woven wire.
Grain
The grain of the paper refers to the direction of the fibers in a sheet of paper. Long grain paper contains fibers which run in the same direction as the longest measurement of the paper. Short grain paper contains fibers run in the same direction as the shortest measurement of the paper.
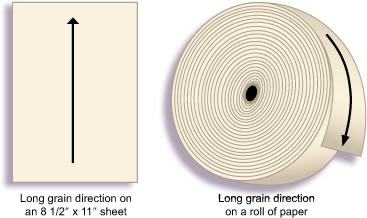
When paper is torn, it will tear easier and straighter when torn parallel with the grain. It will also fold easier parallel to the grain and produce a cleaner fold than if folded across the grain.
p(note) NOTE: Laser printers require long grain paper for the best results. Short grain paper may not feed properly into a laser printer and the heat produced by a laser printer may result in the sheets curling as they come out of the printer.
Whiteness
The whiteness of paper is the measure or its ability to reflect the colors of light equally. The more evenly a paper reflects all colors of the spectrum, the whiter the sheet.
If white paper has a slight warm appearance it will not appear as bright as a sheet that reflects a cool color, however warm colors printed on a warm sheet will appear stronger and cool colors printed on a cool white sheet are also enhanced.
There is no such thing as a pure white sheet of paper, since the white that we see is always influenced by the lighting of our environment and the reflections from surrounding objects.
Grades & Brightness
The grade of a paper refers to the type or category of the paper contents which provide a level of brightness or surface characteristics used to determine the grade level of the finished paper stock.
Grades are classified from “Premium” at the highest level to “5” at the lowest level. Some text and cover stocks are listed simply as A or B grades since fewer grades of the text and cover stock are produced. A table illustrates the grade levels of paper according to the degree of brightness.
Brightness refers to the percent of light reflected back from a sheet of paper as measured by a light meter reading. Contrast is reduced and highlights are not as strong when paper with a lower brightness is used for a printed piece. The grade and brightness of paper is organized into six categories:
Premium | Quality = 88.0 to 95.0 Brightness |
Number 1 | Quality = 85.0 to 87.9 Brightness |
Number 2 | Quality = 83.0 to 84.9 Brightness |
Number 3 | Quality = 79.0 to 82.9 Brightness |
Number 4 | Quality = 73.0 to 78.9 Brightness |
Number 5 | Quality = 72.9 and below |
Opacity
Opacity is the measure (percent) of the amount of light passing through a sheet of paper. Some papers have more fibers and/or fillers and as a result are more opaque than others.
Papers containing more fibers and fillers have the ability to hold a printed image without showing through to the backside as easily as papers without as many fibers and fillers.
Just because a paper is thicker does not guarantee that it is more opaque than a thinner paper. Some thinner papers may be more opaque because there are a greater number of fibers and/or fillers in their composition.
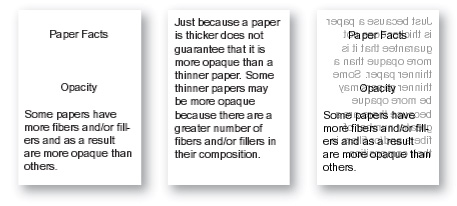
The page on the left shows the front side of a typical sheet printed with black text. The middle page shows text that will be printed on the reverse side of the sheet. The page on the right shows what can happen if the paper is not opaque enough to prevent the backprinting from showing on the front.
Smoothness
The smoothness level is a measure of the surface characteristics of paper. The flatter or more even the surface, the higher the level of smoothness. With a smoother surface, the stock can provide a fully shaped ink dot resulting in a sharper and higher quality image.
Holdout
Holdout refers to the property of ink remaining on the surface of the paper rather than soaking in. A coated glossy paper has a high holdout rate while a paper stock such as newsprint or 20 lb. Bond has a high absorption rate or a low holdout rate.
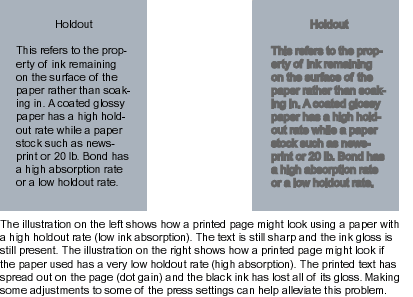
Acidity/Alkalinity
The pH (potential for Hydrogen) measurement of paper determines the degree of acidity and alkalinity in the stock.
Paper can have an acid base, an alkaline base or it can be neutral with a pH of 7. Most paper manufactured in the 20th century was of an acid base. Acidic papers deteriorate in a relatively short period of time, and should never be used for printed items that are intended to last for many years.
The acid level tends to break down the paper and it can deteriorate rapidly, which is why newspapers tend to yellow and fall apart in time. Alkaline paper (a pH above 7) is said to be permanent, but papers that have a neutral pH are still best for preservation.
Conditioning
Paper is very sensitive to changes in temperature and humidity. Excessive moisture will cause flat sheet paper to curl. Many printing companies have temperature and humidity controlled environments to lessen the effects of changing weather conditions.
Paper should always be ordered with enough lead time so that it has a chance to adjust to the temperature and humidity conditions of the printing facility. If you unload paper from a truck that has been in freezing temperatures and then bring it directly to a hot press room, you could have problems.
It is necessary to leave the paper in its original wrapping and let it remain unopened until it becomes conditioned to the humidity and temperature of the pressroom and is ready to be used.
The amount of time necessary for the paper to be conditioned properly can range from a few hours up to several days depending on the amount of paper and the difference in the temperature/humidity between the pressroom and the environment where the paper had come from.
The chart below shows the number of hours necessary for this conditioning.
Paper Quantity | ||||||
---|---|---|---|---|---|---|
(Cubic Feet) | Difference in Temperature | |||||
(From Transit to Pressroom) | ||||||
10° F | 15° F | 20° F | 25° F | 30° F | 40° F | |
6 | 5 hrs. | 9 hrs. | 12 hrs. | 15 hrs. | 18 hrs. | 25 hrs. |
12 | 8 hrs. | 14 hrs. | 18 hrs. | 22 hrs. | 27 hrs. | 38 hrs. |
24 | 11 hrs. | 16 hrs. | 23 hrs. | 28 hrs. | 35 hrs. | 48 hrs. |
48 | 14 hrs. | 19 hrs. | 26 hrs. | 32 hrs. | 38 hrs. | 54 hrs. |
96 | 15 hrs. | 20 hrs. | 27 hrs. | 34 hrs. | 41 hrs. | 57 hrs. |
Types
Papers are often classified according to the properties of the stock and placed into general categories. Two categories in which most papers can be classified are groundwood and freesheet.
Groundwood
Paper stocks are classified as groundwood when they contain more than 10% of their pulp produced from a mechanical process that grinds wood into pulp.
Because all of the wood is used, other ingredients such as lignin and resins are included. These elements are what causes groundwood stocks to yellow quickly and become brittle, so they are good choices for non-permanent printed items such as newspapers.
In addition to this, the wood grinding process produces a pulp with very short fibers so the resulting paper has a low tear strength. Groundwood stocks are less bright and less permanent than paper produced from chemical pulp. Chemical fibers are added to many groundwood stocks to give them added strength.
Freesheet
Freesheet refers to paper that is free of pulp produced from a mechanical grinding process.
Wood chips are cooked in chemical baths which remove the undesirable ingredients such as lignin and resins. Most of the cellulose remains, resulting in fibers that are longer, stronger, and cleaner which produces paper that is brighter and much more permanent than groundwood stocks.
As a subcategory of the groundwood and freesheet paper, stocks can be separated into uncoated and coated stocks.
Uncoated Stocks
Uncoated stock is paper that has no coated pigment applied to reduce the absorbency or increase the smoothness. The uncoated finishes can be described as vellum, antique, wove, or smooth.
Coated Stocks
A coated stock has a surface coating that has been applied to make the surface smoother and more receptive for the reproduction of text and images in order to achieve sharper detail and improved color density.
By adding a coated clay pigment, the objective of coating the stock is to improve the smoothness and reduce the absorbency. Coated paper finishes can be categorized as matte, dull, cast, gloss, and high gloss.
The coating can be on both sides of the stock (coated two sides, “C2S”) or on one side only (coated one side, “C1S”). Coatings added to groundwood papers give them a greater degree of permanency and reduce their natural tendency to yellow over time.
Conclusion
As we have seen, there are many considerations when it comes to choosing paper stock for a printing job. As printers we must have thorough knowledge of these materials as they drastically affect the quality and consistency of our work.
Of course, this is only half of the puzzle, as you will see in the next chapter on Inks.