Coatings
Printed works can be treated with specialized coatings which are often applied in the same fashion that inks are. There are several types of coatings which serve many different purposes.
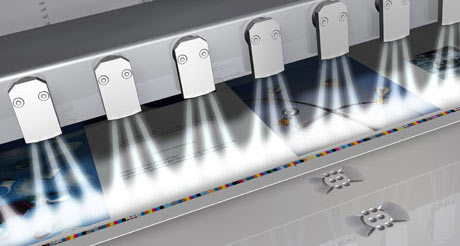
The Coating Process
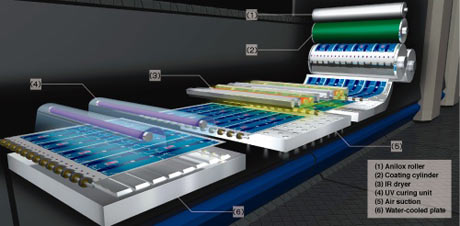
Overprint Varnish
Overprint varnish is available in glossy, dull, or satin finishes and can enhance the look and feel of a printed piece. Besides design effects, another important aspect of varnish is the protection it provides from the wear and tear that of every day handling.
Gloss varnish creates a smooth surface over the paper, filling in any voids or irregularities that may be on the surface. Dull varnish also fills in irregularities to form a smooth surface, but it diffuses light that reflects back to the eyes, which creates a matted appearance. Satin finishes fall somewhere between gloss and dull.
A disadvantage of varnish is that many of them are solvent-based, which means that they emit VOCs during application and require more safety precautions for the press operator.
NOTE: Varnishes made with tung or linseed oil tend to yellow over time if they are formulated. Alkyd formulations will not yellow, but they are not as glossy or as hard as their oily counterparts.
Aqueous Coating
Aqueous coatings are available in gloss, matte, and satin finishes. Among the advantages that aqueous coatings have over solvent-based varnishes is that they will not yellow over time and they are less toxic and emit fewer VOCs.
An aqueous coating is usually applied during the printing process and can be applied as an all-over coat or in patterns or spot coatings. Like varnishes, an aqueous coating offers protection for the printed document and provides numerous effects for print applications.
UV Coating
UV coatings come in a liquid or paste form and remain as a liquid or paste until exposed to ultraviolet light. The printed page is covered with the UV coating and is then exposed to the UV light, which causes photoinitiators within the coating to immediately react, creating a hard protective finish.
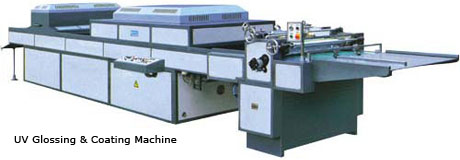
Ingredients called monomers give the coating its gloss and hardness characteristics. UV coating, which is also known as an Energy Curable coating, provides the best surface properties and protection for printed surfaces. Some of the benefits include:
- Greater opacity.
- Color stability.
- Deeper and more vibrant colors and color tones.
- Sharper graphics.
- Higher gloss.
- Uniform surface to give labels a more vibrant look.
- Scuff resistance.
- Instantaneous curing.
- Allows for in-line die cutting.
- Chemical resistance.
- Better outdoor endurance.
- Environmentally safe – No VOCs (Volatile Organic Compounds) are produced.
- EB Ink/Coating
Like UV inks/coatings, EB (Electron Beam) is an energy curable coating, but it is hardened with the use of a concentrated beam of high energy electrons. EB inks/coatings do not contain photoinitiators because the high energy electron beam is all that is necessary to cure the surface.
Other Coatings
Other types of coatings include clay coatings to add strength and gloss to paper, whitewash coatings which are used as a finish coat for such items as Kraft paper, and grease resistant coatings used on applications for industrial and scientific uses.
Spot Coatings
Since varnishes are applied with the same process as ink, a printer is capable of printing various types of coatings on a page. A popular example of this involves highlighting a logo or product with a gloss coating when the rest of the page has a dull finish. The effect of spot coatings makes their respective elements pop off the page
Printed works can also be treated with specialized coatings which are often applied in the same fashion that inks are. When applied as an off-line process over dry ink, they create a bold effect, but when applied as an on-line process, they create a much more subtle effect over ink that is still wet.
Laminating
Description
Laminating is the process of applying a film to either one side or both sides of a printed document. The use of lamination serves several purposes:
Lamination adds luster or gloss to a printed product and stability to the sheet, allowing it to be more durable or stand upright. It also provides protection to sheets that are handled frequently or may encounter moisture. Many laminated documents are waterproof, tear proof, and tamper proof.

Applications
Lamination can be a useful and often necessary addition to various products including posters, maps, membership cards, calendars, food labels, menus, signs, price tags, ID cards, point-of-sale materials, business cards, charts, photographs, placemats, badges, covers, certificates, and many others.
Film Classifications
There are two major categories in which
nearly all types of laminating are classified: pouch and roll.
Pouch
Pouch lamination films are like envelopes and are sealed on one edge. They come in many sizes to accommodate standard items such as letterheads or business cards or they can be made into any custom size.
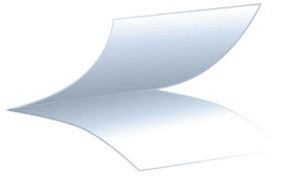
Roll
Roll lamination films can consist of a layer of film that is applied to the front side of a document or it can be two layers of film in which the document is sandwiched between the layers and sealed by the use of various processes.
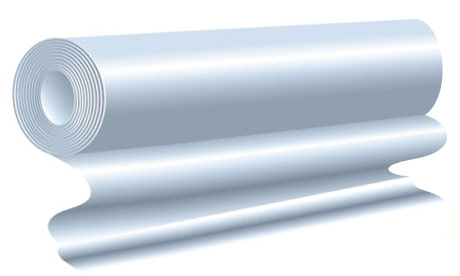
Types of Film
Many of the films used for laminating are available in various thicknesses and finishes ranging from clear gloss to delustered. The three main film materials used for lamination processes are:
- Polyester: A heat resistant, foldable, scuff and scratch resistant, flexible, and tough film. Does not become brittle with age because it contains no plasticizers. Most often used for book covers, folders, and video slipcovers, polyester is the most widely used film.
- Polypropyline: The clearest and brightest type of film and it is used for such applications as posters, labels, marketing, and write on/wipe off calendars. It offers chemical resistance and good optical properties.
- Nylon: Another good choice for applications such as book jackets because of scratch resistance and excellent non-curling properties. When it is exposed to heat, it will not stretch, and when it is cooled, it will not shrink.
Methods of Lamination
Thermal Lamination
The laminate usually consists of 2 plies with each ply made up of an overlaminate film and an adhesive, which is dry and not tacky to the touch. A heat source and pressure are required during the lamination process.
The document is placed between the two plies of the laminate film and then sent through equipment where the dry adhesive is made tacky by heat and is pressed onto the document under high pressure. After cooling, the adhesive solidifies and provides a permanent bond between the document and laminate film.
Cold Lamination
A process in which only one side of a document is laminated. This process is required when the ink and/or paper used for a document is too sensitive to the heat required with thermal lamination. The film used for cold lamination is much more costly than for thermal lamination, but the equipment is less expensive.
One method of cold lamination utilizes a process where no dry adhesive is used. The document surface is flooded with a water-soluble adhesive and is sent through a set of rollers. Pressure is applied which evenly distributes the adhesive and bonds the film to the document.
The adhesive takes a bit longer to cure than thermal lamination and lighter stocks can wrinkle or warp because of the water based adhesive. Cold lamination may not be as permanent as thermal lamination.
Lamination Tips
- Allow several days for laminated sheets to cure, since the adhesive takes time to fully adhere to the stock.
- Use caution when applying a lamination film to varnished sheets. Use a varnish that dries quickly, contains minimal residual solvent, and contains no wax additives.
- Do not laminate printed materials containing metallic inks since air bubbling adhesion problems may occur.
- Use caution when a significant amount of anti-setoff powder has been sprayed on the sheet during printing because it causes adhesion problems.